Closed-End vs. Open-End Horizontal Balers
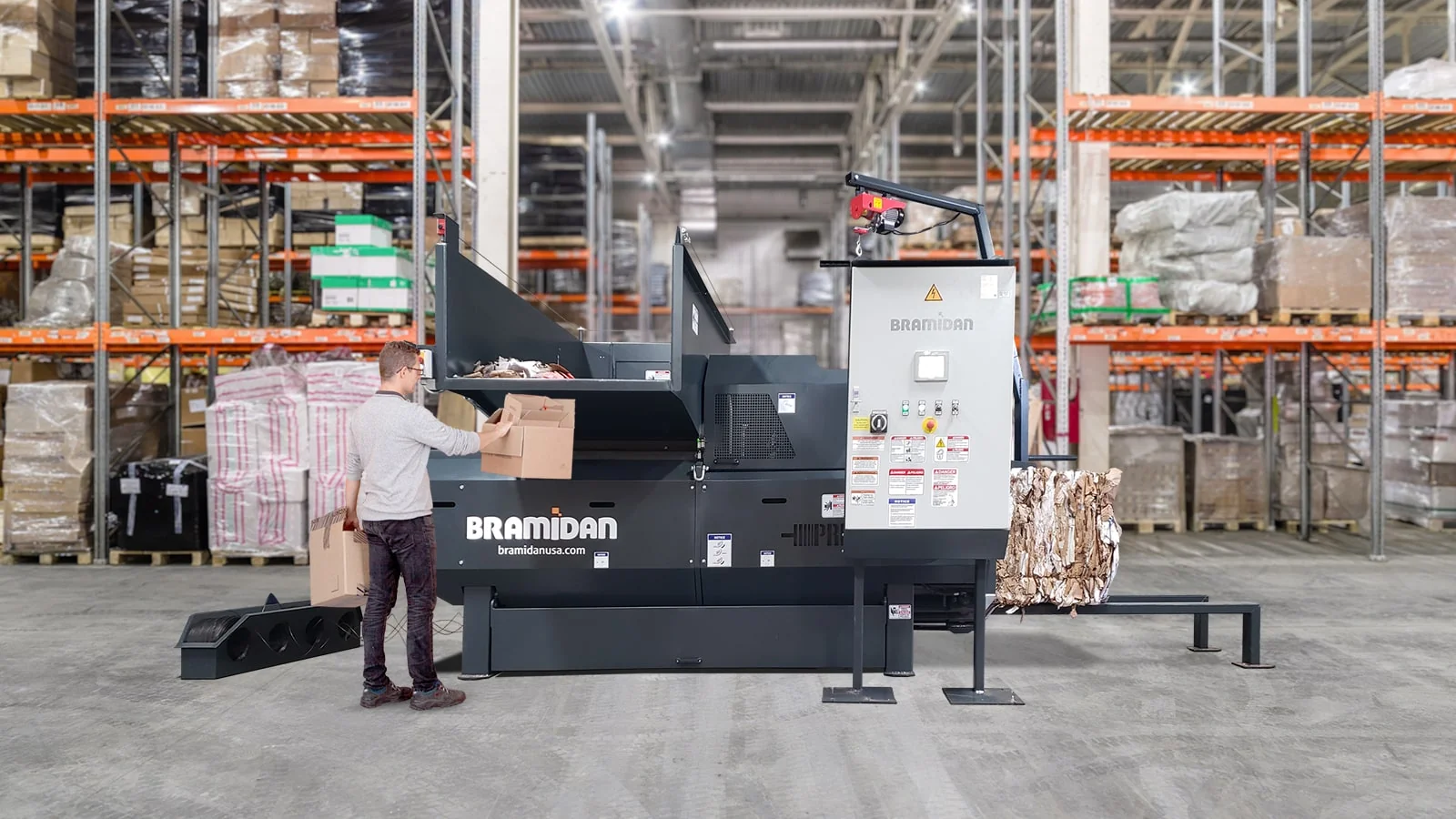
Closed End Vs. Open End – What is The Difference?
Dive into the world of balers as we uncover the key differences between closed end and open end systems. Learn how closed end balers offer versatility and ease of material switching, while open end balers boast automatic tying features. Explore the nuances between these two essential waste management tools and their impact on efficiency.
If you are on a steep growth curve, it may be better to go with an auto-tie open end baler than a closed end. They are more expensive, but you would transition into the larger volumes without having to replace the equipment. The fact is, the busier you get, the more difficult the swap out becomes.
Closed End Balers
Closed end balers are usually used for medium volumes of material and the press forces are typically making bales in the 1,000 lbs to 1,500 lbs range depending on the length and chamber size, cylinder size and other factors.
Additionally, closed end balers are often used when the facility has multiple types of materials to bale, as it is fairly easy to change between materials – for instance cardboard, PET, aluminum cans etc. This is more difficult with an open end baler.
The closed end baler normally pushes out the bales from either the end or the side and generally uses one or two (in a scissor design) cylinder(s).
What Materials are Baled with a Closed End Baler?
Cardboard and paper are the most common materials baled in a closed-door baler due to the amount of crush strength needed as well as the expandability of the materials.
Materials that do not take too much pressure to collapse and maintain a shape are best. However, closed end balers are also very useful for multi material applications with harder materials. Closed door balers are often used in smaller recycling centers and transfer stations, where many different materials are baled every day.
How Does a Closed end (Door) Baler Work?
Think of a vertical baler on its back and that is pretty much a horizontal baler.
Material is fed into an open hopper or funnel that drops the material into a chamber. Behind that chamber is a cylinder and ram that pushes forward and against the end of the baler which is typically a steel gate or solid door.
When the desired size is achieved the baler will reach a predetermined pressure which sets off a signal to light up a finished bale made light. When this occurs, the ram stays forward and the material is tied-off by hand with baling wire. Some models tie vertically and others horizontally depending on the manufacturer and model.
When the bale has been tied, the front gate or door is opened. This can be done manually or with a hydraulic assist, again depending on options chosen and make and model. The bale is pushed out either by an extending cylinder or by the ram retracting and more material being added until the bale is pushed out.
On average, a closed-end baler generates up to 3 bales per hour and is recommended for processing and compacting low to moderate volumes of cardboard or paper waste, as well as aluminum cans, PET bottles, stretch wrap etc.
Baler Door & Manual Tying
After the baling process has been completed, the bale needs to be manually tied off by the operator. The rear or side door can be opened when finished, so the pressure is released inside the channel. The bale is then pushed out by extending the ram or by the next bale that is in production. This type of baler can be used for single-bale output.
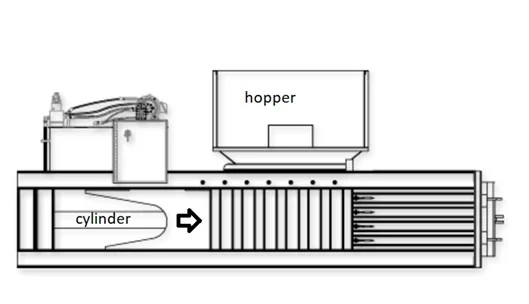
Open End Balers
Open end balers are also usually auto-tying balers that will tie the bales together automatically; whereas bales made in a closed door baler typically have to be tied manually, by hand.
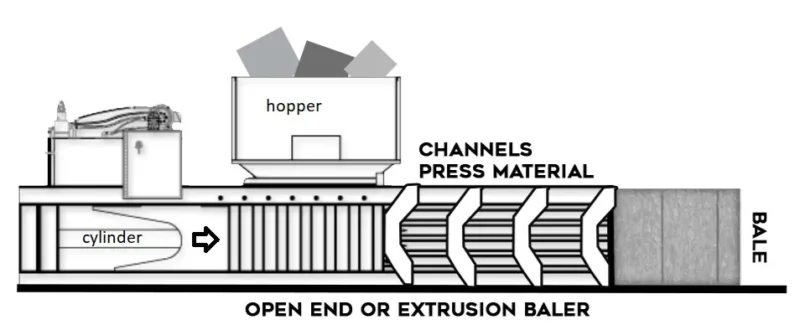
Fill in the form and we will contact you
Questions? Contact Us Today
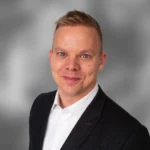
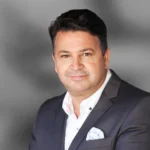
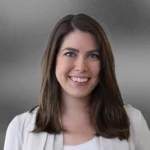
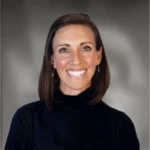